Midas BioTech
Sustainably Turning Waste Into Wealth
Midas BioTech
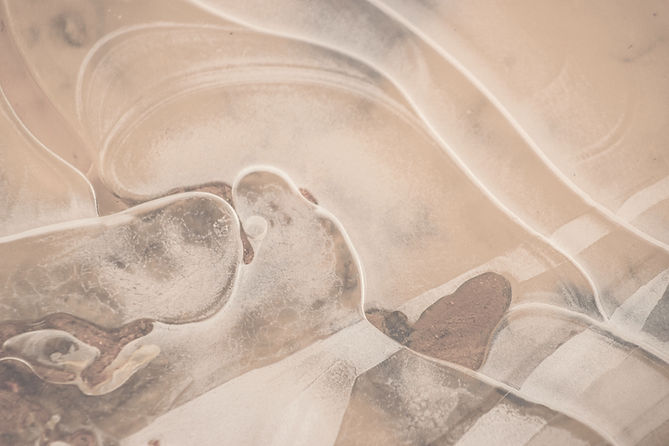
Our Process
Our metal bioleaching process is a sustainable and innovative solution for recovering valuable metals from e-waste. By using specialized and genetically engineered bacteria, we efficiently extract copper and precious metals like gold and silver in an eco-friendly manner, reducing reliance on harmful chemicals. This stepwise approach maximizes recovery rates, minimizes waste, and supports a circular economy, offering a cleaner, more sustainable alternative to traditional recycling methods.

01
Waste Collection
The first step in the metal bioleaching process involves sourcing electronic waste (e-waste) from various collection points and suppliers. We partner with waste collection centers, recycling programs, and businesses to gather discarded electronic devices such as computers, smartphones, and circuit boards.
02
Sorting E-waste
The collected e-waste is carefully sorted to isolate metal-containing components. Manual or automated dismantling of devices to retrieve circuit boards, wires, and other components are dismantled to keep parts rich in metals like gold, copper, and silver. Non-metallic materials such as plastics, glass, and rubber are set aside for independent recycling.


03
Pre-processing
The remaining e-waste is shredded with stainless steel blades and further crushed into fine powder. The remaining microscopic particles are collected, washed, dried and sterilized to prepare for bioleaching. The metal content of the metallic powder is characterized using spectrophotometry and chemical techniques to measure metal concentration and purity.
04
Metal Bioleaching
This powder undergoes a two-step bioleaching process. First, acidophilic bacteria are used to leach copper. This step also removes copper as a competing metal, enhancing the efficiency of subsequent leaching processes. The residue is treated with a genetically engineered bacterium in a glycine and thiosulfate-rich reactor to leach precious metals such as gold and silver.


05
Extraction
After bioleaching, metals are extracted from the leachant using a foam fractionation column, an eco-friendly and efficient separation technique. The process involves introducing air or gas bubbles into the leachant, which selectively binds metal ions to surfactants, forming a stable foam. This foam, enriched with metal ions, is then collected and processed to recover purified metals.
06
Distribution
